PioCreat Wraps Up I.S.P.O. WORLD CONGRESS 2025
piocreat3d on June 23, 2025
PioCreat proudly concluded a successful showcase at the 20th I.S.P.O. World Congress, held from June 16–19, 2025, in Stockholm, Sweden. The International Society for Prosthetics and Orthotics (ISPO) World Congress is a premier global event bringing together leading experts in prosthetics, orthotics, rehabilitation engineering, and related fields. With over 3,000 members across 90+ countries, ISPO fosters collaboration and innovation in restoring mobility and improving lives.
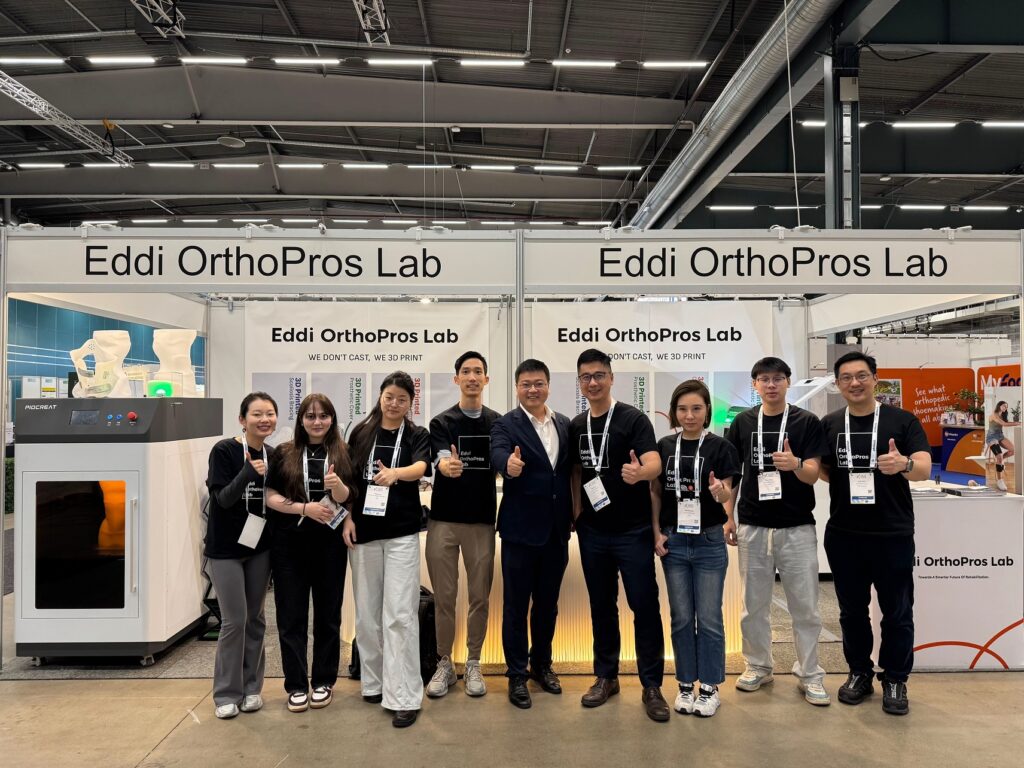
Throughout the congress, PioCreat engaged with industry professionals, clinicians, and researchers, highlighting how additive manufacturing is reshaping prosthetic and orthotic solutions. Our booth showcased advanced 3D printing applications designed to deliver precision, customization, and efficiency to the field.
We were delighted to connect with partners such as Eddi OrthoPros Lab and Foothealth UK, who joined us at the event for valuable discussions and collaboration.
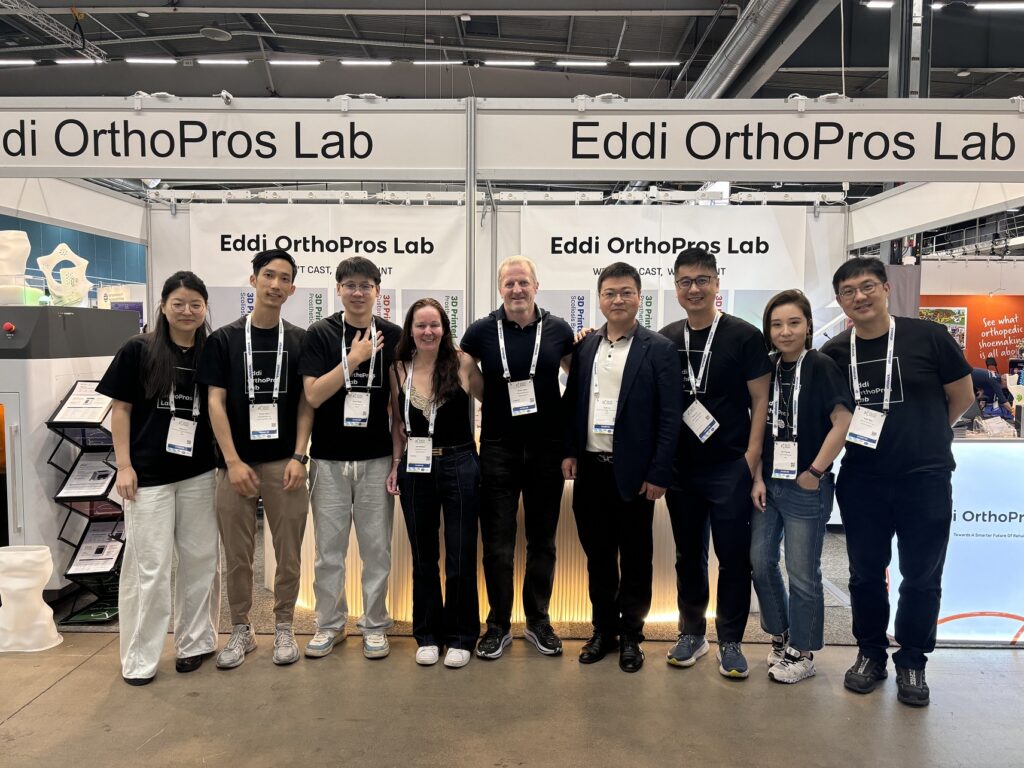
Key Highlights of Our Solutions
Scoliosis Brace Production: The MS01 high-temperature pellet 3D printer demonstrated its capability to produce fully customized spinal orthotics with superior support, comfort, and fit.
Custom Insole Fabrication: The IPX2 3D printer, combined with our FS A003 foot scanner, provided a streamlined digital workflow for designing and manufacturing personalized insoles with precision and speed.
Prosthetic Sockets and Covers: Our custom-engineered 3D printed prosthetic sockets and covers deliver greater durability, comfort, and aesthetic flexibility compared to traditional methods. Material and color options allow for enhanced personalization while reducing limb wear and improving stability.
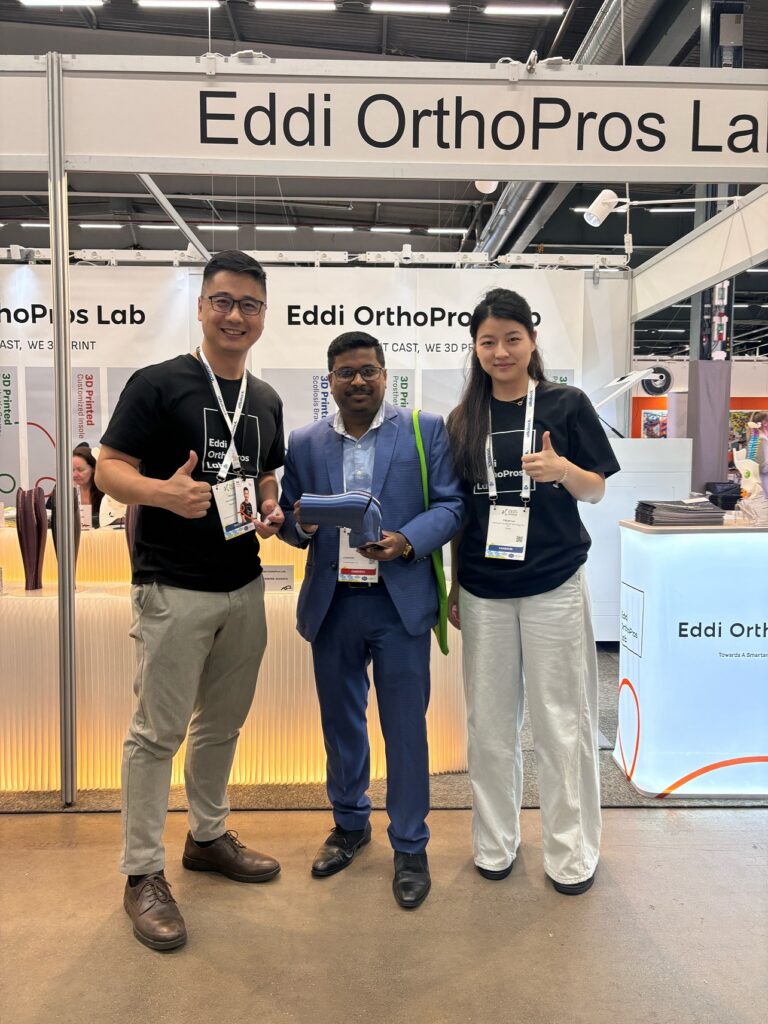
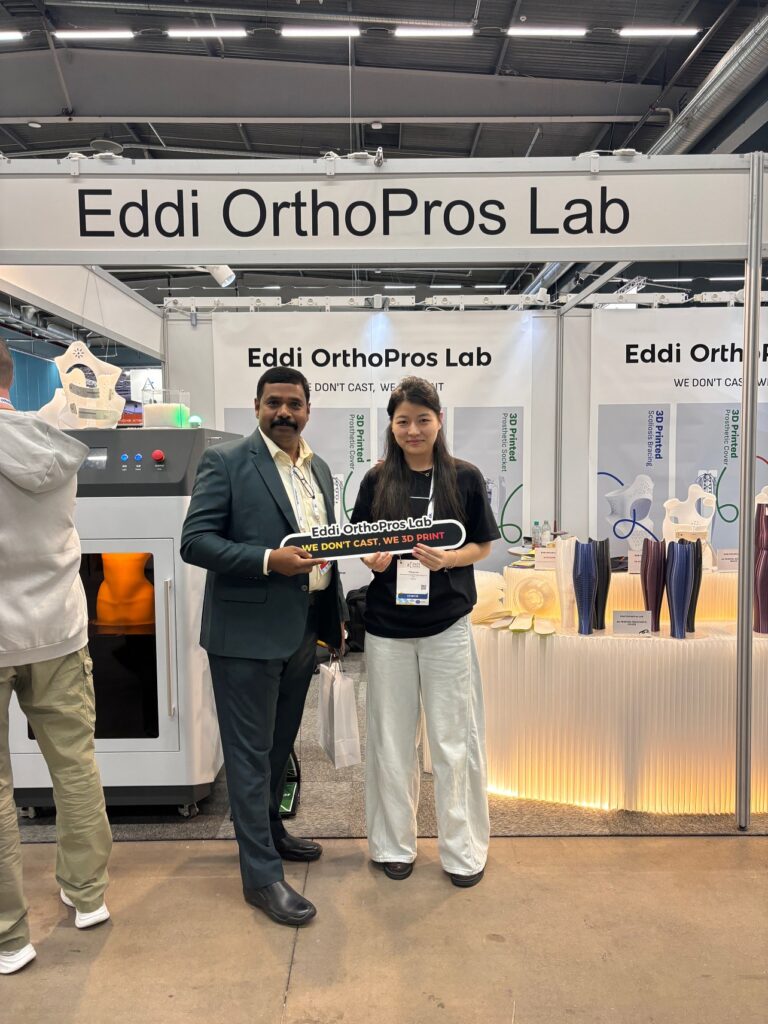
PioCreat remains committed to advancing digital manufacturing solutions that support clinicians and improve patient outcomes in prosthetics and orthotics.